In order to safely manage and control their liquid inventory, chemical and petrochemical manufacturers require accurate, repeatable gas flow and dependable pressure monitoring to determine liquid level measurement in their tanks, vessels, or barrels. A Brooks Instrument glass tube variable area flow meter, a manual flow controller, and pressure transducer all work together to accomplish this.
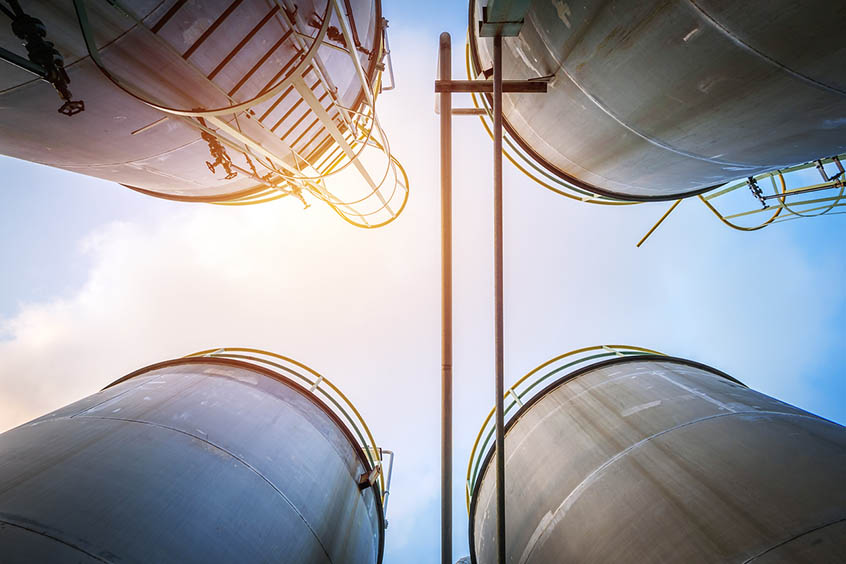
Application
In order to measure the liquid level in the tank, the pressure created by the weight of the liquid must be determined by a pressure transmitter. The pressure measured at the bottom of a tank of liquid will be proportional to the level of the liquid in the tank according to the relationship: Height of liquid = Pressure at bottom of tank/density of liquid. Specifically, the SolidSense II® pressure transducer from Brooks Instrument supports the process by taking measurements of the weight of the liquid.
Instrument Highlights
- High performance integral flow controller improves the accuracy of flow measurement
- Instrumentation suited for multiple pressure ranges
Process Solution
A small diameter (typically ¼’’) tube or “dip tube” is installed in the tank, extends into the liquid, and sits near the bottom of the tank. The Brooks Instrument Sho-Rate™ Series glass tube variable area flow meter accurately measures a repeatable low flow rate of Nitrogen or air flowing into the "dip tube". Once the gas flow reaches the bottom of the tube, the gas will transfer the pressure at the bottom of the tank to the tube's inlet. With fluctuations in pressure near the inlet, while maintaining a low-pressure drop low in the tube, a flow rate of 1.0 SCFH is typical for a ¼" diameter "dip tube". This flow rate minimises the offset in the level measurement created by this pressure drop.
With pressure fluctuations and varying liquid levels in the tank, the FC8900 integral downstream flow controller from Brooks Instrument works in tandem with the Sho-Rate™ variable area rotameter to keep the gas flow rate constant. It is important to note that the supply pressure to the glass tube variable area rotameter should be set to a value high enough to overcome the back pressure of the liquid level and the minimum pressure drop needed across the flow controller for full functionality. A supply pressure of 25 psig would be adequate for tank levels up to 30 feet. The flow meter scale should be sized (i.e. compensated) for this supply pressure. This further improves the level measurement by keeping the offset constant.
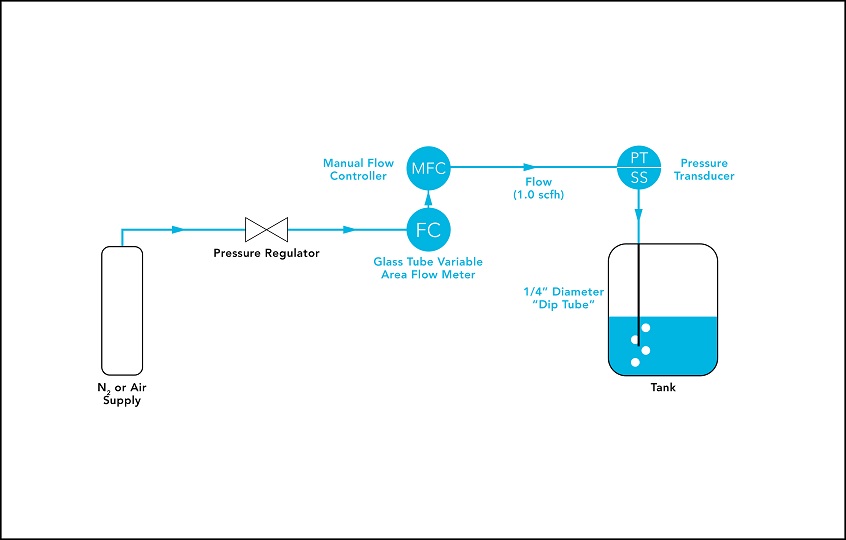
Flow Scheme
For chemical and petrochemical manufacturers, measuring, monitoring and controlling liquid level is crucial for their operations. The instrumentation from Brooks Instrument such as the Sho-Rate™ glass tube variable area flow meter, FC8900 manual flow controller, and SolidSense II®; pressure transducer are recognized for accuracy and repeatability for low flow rates especially for an application with varying pressures such as the measurement and control of liquid levels.
Component datasource missing. Select a datasource for this component.